All-Welded Attached to Supported Clip Angles
- General Overview
- Tips and Tricks
- Related Tools
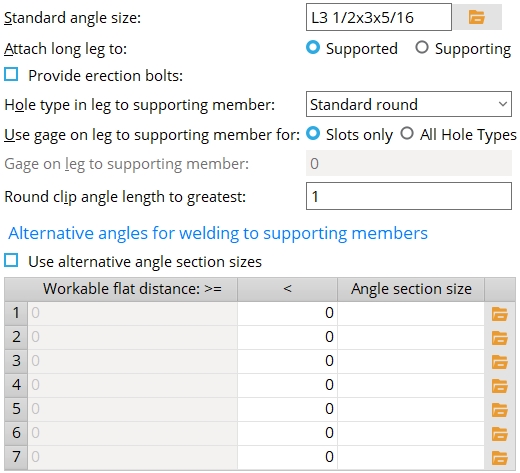
To specify this type of standard clip angle in the model :
- All-Welded Attached to Supported Clip Angles are double clip angles that shop weld to the supported beam. They are designed as the supported beam's end connection when ' Supported ' (shop attached to), ' Welded ' (to supported) and ' Welded ' (to supporting) are set in "
Connection specifications " for auto standard , user defined or beam-window-specified clip angles.
- You can get a clip angle hanger connection for a column by selecting ' Clip angle ' as the column's " Input connection type " then checking the box for "
Force ."
Standard angle size: The preferred angle section size . The angle must be listed in the local shape file. Note that alternative angles can also be specified on this window.
To enter an angle section size: Either type in the section size that you want (e.g., ' L4x3 1/2x5/16 '), or press the "file cabinet" browse button (
) and choose an angle section from the list of angles in the local shape file .
Attach long leg to: Supported or Supporting . This applies when a " Standard angle size " with unequal legs has been entered.
' Supported ' shop welds the long leg of the angle to the supported beam.
' Supporting ' field welds the long leg of the angle to the supporting beam or column. Erection bolts can also, optionally, be provided for field bolt attachment of each to-supporting leg.
Provide erection bolts: or
. This sets whether or not erection bolts are provide when ' Automatic ' is the choice made to " Use erection bolts " in the
Connection specifications "
If this box is checked (
), erection bolts are provided. For a beam end connection that is not auto standard, the bolts are the "
Connection type " > " NM bolt type to supporting " and " NM bolt diameter " that are specified for that beam connection's end. Erection bolts are field bolts. For an All-Welded Attached to Supported Clip Angles double clip angle connection, four erection bolts are required, two for the NS OSL plus two for the FS OSL.
If the box is not checked (
), the All-Welded, Attached to Supported Member clip angles are designed without erection bolts.
Hole type in leg to supporting member: Standard round or Short slot or Long slot or Oversized or User slot #1 or User slot #2 .
Use gage on leg to supporting member for: Slots only or
All hole types .
'
Slots only ' instructs connection design to apply the " Gage on leg to supporting member " only when the " Hole type in leg to supporting member " is ' Short slot ' or ' Long slot ' or ' User slot #1 ' or ' User slot #2 '.
'
All hole types ' instructs connection design to apply the " Gage on leg to supporting member " for all hole types, including standard round holes.
Gage on leg to supporting member: The distance from the outside corner of the clip angle to the center of the column of slots on the outstanding leg (on the leg with erection bolts to the supporting beam or column).
For slots, connection design may apply a different GOL than that which is entered here in order to permit bolts to fit into the slots at the "Narrow gage" center-to-center hole distance.
Round clip angle length to greatest: The distance by which you want connection design to increment the length of clip angles (e.g., 1/2 makes connection design round angle length up to the nearest half inch).
Alternative angles for welding to supporting members
Use alternative angle section sizes: or
.
If this box is checked (
), connection design looks at the workable flat distance on the face of the supporting member that the double clip angles are to be field welded to, then selects the angle from the alternative angles table.
If the box is not checked (
), connection design uses the " Standard angle size ."
Workable flat distance is greater than or equal to
( >= )Workable flat distance is less than
( < )Angle section size The values in the first column are filled in automatically. They represent the lowest workable flat distance at which the " Angle section size" entered in a particular row will be applied.
The values in the second column can be filled in manually. Each such value represents the largest workable flat distance at which the " Angle section size " entered in a particular row will be applied. The angle to be welded within the workable flat distance on the supporting member. You need to account for the welds and the thickness of the supporting beam's web as well as the angle leg size when determining if the angle will fit in the specified workable flat distance.
![]()
![]()
![]()
![]() |
|
OK (or the Enter key) closes this screen and applies the settings.
Cancel (or the Esc key) closes this screen without saving any changes.
Reset undoes all changes made to this screen since you first opened it. The screen remains open.
- Clip angle input specs (settings for clip angles)
- Setup of clip angle connections (index)
- Clip Angle Settings